Kazakh scientists are developing a set of technologies for producing the endoprostheses that consider patients’ pecularities
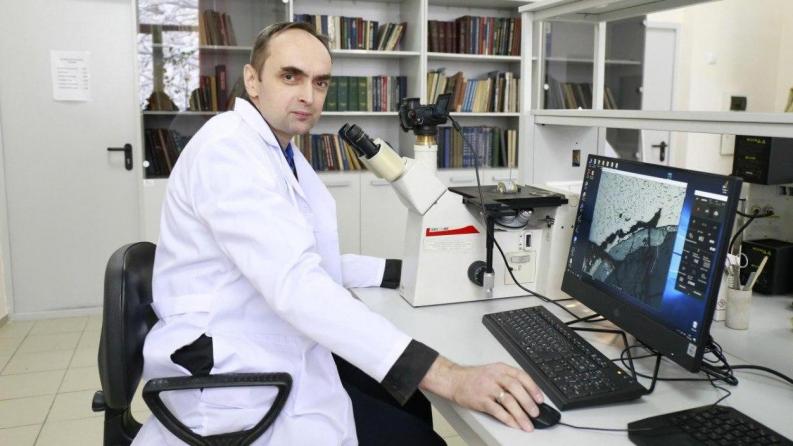
Metallology laboratory of Metallurgy and Enrichment Institute at Satbayev University is developing new technologies and equipment for producing the individual endoprostheses.
A special furnace has been created for melting titanium alloys. It operates in the vacuum and uses a tungsten electrode. The main goal is to obtain molten titanium material, which can then be poured into a mold. Maximum mass of molten titanium that can be produced using this furnace is 2 kilograms. Furnace is equipped with the efficient air pumping system, as well as the power supply with adjustable power.
Low-tonnage melting and casting of titanium alloys, technology and molding materials for casting burnt models, magnetron and microplasma application of calcium phosphate biocompatible coatings on the surface of endoprostheses can accelerate the process of fusion with bone tissue, reduce allergic reactions of the body.
Process of applying biocompatible calcium-phosphate coatings due to magnetron and microplasma coating methods to titanium alloy endoprostheses is carried out at the magnetron sputtering plant and microplasma oxidation plant developed at Metallurgy and Enrichment Institute.
For the first time, materials based on calcium titanate with an environmentally friendly binder are proposed, which ensures the solidification of the mold at the temperature of maximum expansion of the casting model. For maximum protection against the interaction of the mold with titanium melt, a barrier paint based on yttrium oxide has been elaborated to apply it to the casting model’s surface.
Currently, the production of endoprostheses for restoring the joints of the human skeleton is widely established in the world. However, if the damage to the skeleton is not caused by typical causes, standard endoprostheses cannot be used. Such injuries can occur when bone tissue is damaged by oncological diseases, in car accidents, as a result of industrial injuries, or with shrapnel and bullet wounds. In this case, elaborating the individual endoprosthesis is necessary.
Presently, endoprostheses made of titanium alloys are most widely applied that is explained by the bioinertness of the given metal, owing to formation of a thin dense layer of titanium oxide on its surface. However, in the liquid state, such metal is characterized by the highest activity. This makes melting and casting of titanium alloys extremely difficult and requires the use of special equipment, technologies and materials. This task is successfully solved by the new development of scientists from Metallurgy and Enrichment Institute at Satbayev University, namely, Head of Metallology laboratory: candidate of physics-maths sciences, associate professor Aksaule Mamayeva, candidate of technical sciences Alexander Panichkin, researcher, PhD Aidar Kenzhegulov, smelter, junior researcher Zhasulan Alibekov.